材料实验复习笔记
文章目录
复习时间实在紧迫,草草完成,未经校对。
金相磨制与观察
金相显微镜
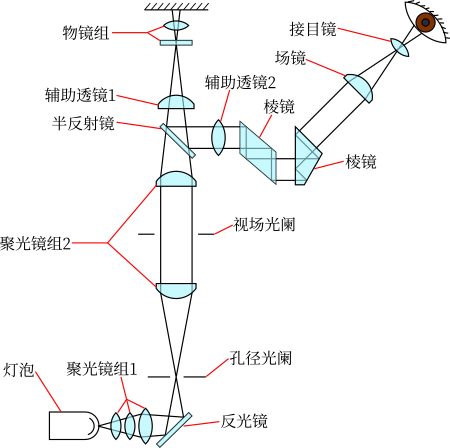
金相显微镜结构
- 使用步骤:放样→低倍观察→高倍观察→降低载物台→低倍→取样
- 拍摄次序:预览→调焦→曝光时间→白平衡→拍摄→标尺→保存
- 思考题
- 提高显微镜分辨率:不要求色彩时,使用紫光作为光源。
金相样品制备
- 磨制:
- 砂纸由粗到细(编号由小到大),越细越不能用力。
- 磨制前先倒角。
- 打磨→磨至出现一致均匀分布的细小磨痕→水洗,更换砂纸,试样旋转90°,打磨。
- 抛光:
- 在抛光机圆盘中间区域涂抹一定量抛光膏。
- 在抛光盘1/2半径处抛光。
- 抛至获得光滑、无痕的镜面,水洗。
- 腐蚀:
- 酒精洗→吹干→放入4%硝酸酒精溶液腐蚀3s→水洗 →酒精洗→吹干
- 腐蚀时间随碳含量升高而升高,未知样品则腐蚀至表面颜色稍有变暗,出现彩色即为过腐蚀。
- 低倍镜深腐蚀,高倍镜浅腐蚀。
- 思考题:
- 试样选择的基本要求:取样部位必须与检验目的和要求一致。
- 表面热处理的齿轮如何取样:切取φ12×12 的圆柱体或 12×12×12mm 的立方体,注意冷却和润滑,严禁倒角。
- 制备中易产生哪些假象:高温灼伤→空洞/疏松;粗大划痕抛光后遗留小黑点→夹杂物脱落;抛光掩盖夹杂物/空洞/石墨色彩→混同。
铁碳金相
金相组织中最简单的是单相多晶体等轴晶粒组织。
- 其中可见亚晶界,亚晶界稳定,但形变热处理+再结晶可消除,是过饱和固溶体分解时优先形成沉淀相的地方。
- 冷却速度慢,形核数量少,晶粒较大。
铁碳相图

Fe_C相图
渗碳体是强化相,增加强度与耐磨性,铁素体提供塑性。
非平衡组织
- 贝氏体:过冷奥氏体中温转变产物,转变温度低于珠光体转变。下贝氏体转变温度较低,具有很好的综合力学性能。
- 马氏体M:C在α铁中的过饱和固溶体,转变温度低于贝氏体相变。硬度和强度很高,塑性差。
金相组织形态
用硝酸酒精溶液腐蚀,铁素体和渗碳体均呈白色,而晶界易被腐蚀而凹陷,呈现黑色。珠光体、铁素体一般为块状,渗碳体一般为条状或沿珠光体晶界。亚共晶白口铸铁中会出现γ枝晶(常温下转变为珠光体)。
用苦味酸钠腐蚀,渗碳体呈黑色。
铝硅金相
硅可以提升流动性,改善铸造性能;富硅相硬度较高。
金属铸态组织
- 一元:分为细等轴晶区、柱状区、粗等轴晶区。粗大柱状区降低力学性能,应细化晶粒。
- 二元:易产生枝晶偏析,可以退火消除。快速冷却,枝晶细小,退火时间缩短。
非平衡凝固
- 共晶生长过程中,β(Si)相领先,这是因为Al-Si系共晶界面的过冷度主要来自于成分过冷而非动态过冷。
- 伪共晶:由非共晶成分在非平衡冷却条件下所得到的全部共晶组织称为伪共晶。两组元熔点相近,伪共晶区对称,否则偏向高熔点一侧。因而Al-Si在共晶成分会得到亚共晶组织。
- 非平衡共晶:非平衡条件下固相线偏离,且铸模冷却有定向散热特征,使得应为单相的成分出现了少量共晶组织。
- 离异共晶:因为共晶数量少,占大量的α依附于已析出的α生长,将占少量的β推至凝固晶界处,共晶特征消失。但是在平衡凝固中也可出现离异共晶。
- 共晶成分的Al-Si合金中由于局部的成分差异而出现小块状的初生硅相。由于硅的析出,周边形成α相的晕圈。
变质处理
在熔融合金中加入少量的一种或几种元素(或加化合物起作用而得),改变合金的结晶组织。
加入少量其他元素后,形成高熔点的固相质点,具有与纯铝相同的晶格类型与相近的晶格常数,可以作为形核。因而共晶硅由针状变为细粒状。
金属组织形态
初生硅为黑色小块状或块状,共晶硅为黑色针状;α相为白色,可能出现枝晶。
回复再结晶金相
塑性变形对材料的影响
- 显微组织:晶粒内出现大量的滑移带、孪晶带;等轴晶粒逐渐沿变形方向伸长,形成纤维组织
- 亚结构:形成位错缠结,胞状亚结构
- 性能:密度下降,加工硬化,电阻率上升
- 形变织构:晶粒出现择优取向
- 残余应力:宏观残余应力,微观残余应力,点阵畸变
回复再结晶
回复
内应力释放,电阻率下降,晶粒形态不变,硬度不下降。
- 低温回复:点缺陷迁移
- 中温回复:位错运动和重新分布
- 高温回复:应变能驱动,刃位错攀移,形成位错墙
再结晶
形核:低温下晶界弓出,高温下亚晶合并。其驱动力是畸变能降低。
再结晶温度:冷变形金属开始再结晶的最低温度,与变形程度(越大越低)、原始晶粒尺寸(越小越低)、杂质原子等有关。
再结晶晶粒大小:低于临界变形度,不发生再结晶;高于临界变形度,晶粒粗大,随变形度上升,再结晶晶粒细化。因而要避开临界变形量。此外,温度越高晶粒越粗。
晶粒长大
正常长大:
- 驱动力是界面能降低
- 由于晶界曲率不同,大角度晶界迁移
- 温度越高越快,分散相粒子和杂质元素越多越慢
异常长大(二次再结晶):
- 驱动力是界面能降低
- 有二次再结晶温度
- 以一次再结晶后的某些特殊晶粒为基础长大
热加工
高于再结晶温度即为热加工,硬化与软化同时存在。可以消除铸造中的某些缺陷和偏析,比铸态有较好的力学性能。
动态回复:
- 发生于高层错能金属,滑移和攀移容易进行
- 出现加工硬化→出现回复软化→达到平衡,稳态流变
- 晶粒伸长呈纤维状,内部却保持等轴亚晶无应变的结构
动态再结晶:
- 发生于低层错能金属,滑移和攀移难以进行
- 出现加工硬化→出现再结晶软化→达到平衡,真应力可能震荡
- 晶粒内还有被位错分割的亚晶
组织观察
可以采用直径测定法估测晶粒直径。
思考题:
- 硬度是否材料常数:硬度不是材料的本质参数,它会随材料处理方式的不同而不同。硬度数值与压头试验力试样状况都有关。
- W丝中容易产生大晶粒从而在热冲击下破裂,试介绍一种续命方法:可以细化晶粒;可以加入弥散分布的第二相(如\(ThO_2\)),阻碍晶粒长大。
硬度测试
各种方法的总对比:
项目 | 布氏 | 洛氏 | 维氏 |
---|---|---|---|
压头 | 淬硬钢球/硬质合金球 | 120°金刚石圆锥/$$1.588mm淬硬钢球 | 金刚石正四棱锥体 |
表示方法 | 硬度 HB压头种类(S/W) 直径 /压力 |
硬度 HR标尺(A/B/C) |
硬度 HV压力 |
测量量 | 压痕的两条直径 | 残余压入深度e | 压痕的两条对角线长 |
计算公式 | \(HB=\frac{2P}{\pi D(D-\sqrt{D^2-\bar{d}^2})}\; kgf/mm^2\) | \(HR=\frac{K-e}{0.002},K=0.2mm\:\mathrm{or}\:0.26mm\) | \(HV=\frac{1.8544P}{\bar{d}^2}\; kgf/mm^2\) |
优点 | 反应平均性能;数据稳定;可估算\(\sigma_b\) | 操作简便,压痕小 | 可测各种材料,压痕清晰,标度统一 |
缺点 | 不能测太硬材料;压痕大;测量繁琐 | 代表性差,不同标尺不能直接比较 | 代表性差 |
布氏硬度
测试要求:
- 压痕半径与压头半径满足\(0.24D<d<0.6D\)
- 满足几何相似性要求,即\(\frac{P}{D^2}\)为标准值
- 试样厚度不小于压痕深度的10倍
- 试样越软,保持时间越长
- 两条直径差距不超过2%
测试时需手动施加预载荷,需手动测量
洛氏硬度
测试要求:
- 先加初载荷,压入深度\(h_0\) ;再加主载荷,再卸去主载荷,压入深度\(h_2\) ;\(e=h_2-h_0\)
测试时需手动施加预载荷
维氏硬度
测试要求:
- 试样厚度不小于压痕对角线的1.5倍
- 试样越软,保持时间越长
- 两条直径差距不超过2%
要先校准调零,测试时需手动测量